Kindbot moves into a new Shell
Making Kindbot more efficient
The Kindbot Exoskeleton
Our first attempt at a 3D print case reflected the flexibility of extra USB ports, cpu cores, and space for extra wiring.
The time has come for Kindbot to reduce its footprint. We began with a complete redesign around the Raspberry Pi Zero. But instead of simply encasing the embedded device, we chose to retract in all sensors and cameras from the original design.
This sleek design would be necessary to protect the wiring and sensors and is expected in a consumer product. We began with rudimentary shapes using tinkerCAD, gluing blocks together and slicing chunks away to carve out the new Kindbot shell.
We found a fantastic 3D print ball joint to allow the shell to swivel for framing the shot. The printed tube clamp is sized for standard grow tents with a rubber bushing.
We created a notch to slide the Kindbot access panel into position, a small knob on the back clicks into the socket joint for attachment options. We have also created a strap clip for other mounting options.
Our first custom design came out nearly perfectly. The USB and power ports needed some adjustments and we ordered a more minimal picam so that we could reduce the shell size further still.
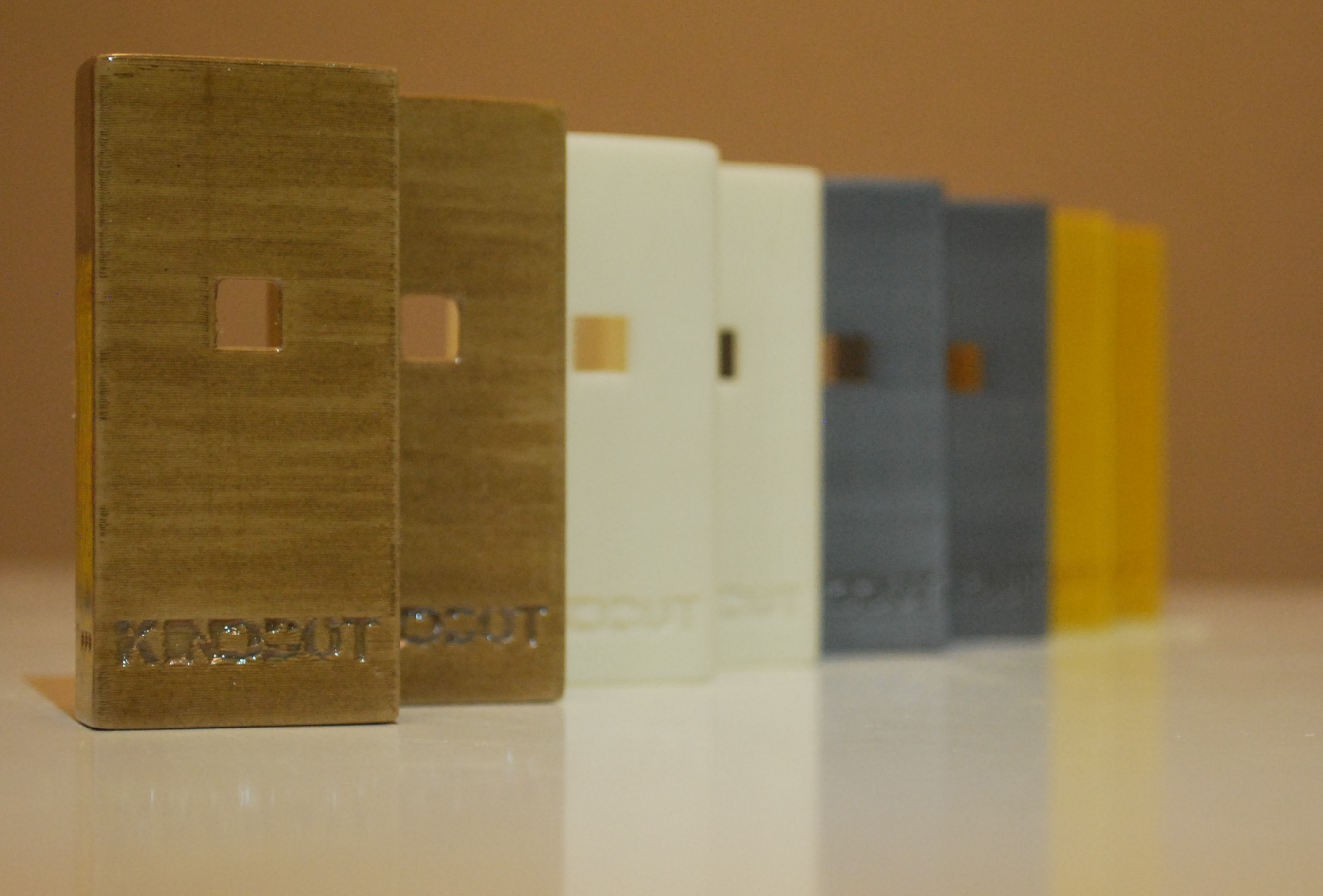